建築材料や自動車、航空・宇宙、スポーツ用具など様々な分野で注目されている、軽くて丈夫な「繊維強化複合材料」。 現在、そしてこれからも活用分野の拡大が予想される繊維強化複合材料を専門に研究されている、北海道科学大学 工学部 機械工学科の太田 佳樹教授にお話を伺いました。
「繊維強化複合材料」は、土壁と原理は同じ
Q:まず、太田教授が研究されている「繊維強化複合材料」とは何か、簡単に教えてください。
太田:複合材料というのは、2つの異なる材料を組み合わせて一体化し、元の素材だけでは成り立たなかった性能を生み出そうというものです。私がメインで研究しているのは、プラスチック樹脂の中に繊維が入っている繊維強化プラスチック(FRP:Fiber Reinforced Plastic)というものですね。
いちばんの特長は軽くて強い材料という点で、鉄やアルミニウムなどの代用品として1960年代頃から研究が進められてきている素材です。この数十年で自動車部品、航空機の胴体や主翼、スポーツ用具などに使用されるなど、実用域になってきたと思います。
でも実は、昔から日本の家屋に使われていた土壁、あれがもう複合材料なんですよ。土壁の場合、まず竹を編んで下地を作りますが、竹だけでは家は造れません。屋根の重さを支えることはできても、熱や音などを通してしまい密閉することができません。一方、土だけですと、熱や音は通さないけれども屋根の重さを支えることはできません。そこで竹を編んだ周りに土を固めて造るのが土壁なんです。
Q:繊維強化プラスチックも原理的には似たようなものなのでしょうか。
太田:全く同じと言っても良いと思います。今は竹の代わりに、炭素繊維やアラミド繊維・ガラス繊維など、金属材料よりも引きちぎりにくい強さのある材料を使っています。そして土の代わりにプラスチック樹脂を使っています。プラスチックの中にヒモのような繊維が入っているイメージです。
あと、繊維強化複合材料にもいくつか種類があって、プラスチックのかわりに金属を使うやり方もあります。金属の中に炭素繊維を埋め込んだFRM(Fiber Reinforced Metal)は、車のコンロッド(エンジンのピストンとクランクシャフトをつなぐパーツ)などに使われているようです。
異なる性質をもつ2種類の繊維強化プラスチック
Q:繊維強化プラスチックの性質とはどのようなものかお聞かせください。
太田:繊維強化プラスチックにも種類がありまして、「熱硬化性樹脂」と「熱可塑性樹脂」の2つがあります。
熱硬化性樹脂は一定時間加熱することで硬化する樹脂で、これまで一般的にFRPと言われているのはこちらになります。技術的に成熟してきているもので、有名なところではエポキシ樹脂などがあり、接着性が良くて耐熱性、耐湿性に優れています。ただし、一度成型すると加工し直すことができず、リサイクル性もありません。
一方、熱可塑性樹脂は、広義的にはFRPなのですが、熱硬化性樹脂と分ける意味でFRTP(Fiberglass Reinforced Thermoplastic)と呼ばれています。熱を加えると柔らかくなり、冷やすと固まる性質をもつ樹脂です。一般的に普及しているナイロンやポリエチレンなども熱可塑性樹脂で、何度でも加熱して再成形が可能です。加工や再利用がしやすいため現在研究が進んでいる素材です。
Q:どのような分野に使用されているのでしょうか。
太田:熱硬化性樹脂については、アメリカでは航空・宇宙の分野での需要が多く、日本の場合にはスポーツ用品での使用が盛んですね。ほかにも船舶のボディや建材・風力発電のブレードなどにも使用されています。最近では、車体を軽くするために自動車メーカーがどんどんFRPを導入しています。
また、ペットボトルや食品トレーなど、一般的に普及しているプラスチックは熱可塑性樹脂になります。熱硬化性樹脂に比べ加工がしやすくて大量生産にも向いているため、こちらも自動車メーカーが主導で研究を進めていますね。
Q:エレベーターへの活用はされているのでしょうか。
太田:通常のエレベーターの場合、コスト的にまだ難しいかもしれません。ただ、私は専門ではないのですが、新しい複合材料の研究が進んだ結果、宇宙エレベーターも実現味を帯びてきたようです。宇宙エレベーターについてはかなり昔から研究がされていますが、例えば宇宙から地上まで吊り下げられる長いケーブルを作るには、通常の鋼のケーブルでは自重で引きちぎれてしまうため、実現が不可能だったのです。しかし、研究によって開発された新しいFRPを用いたカーボンナノチューブによって、宇宙エレベーター実現への光明が見えてきたようですね。
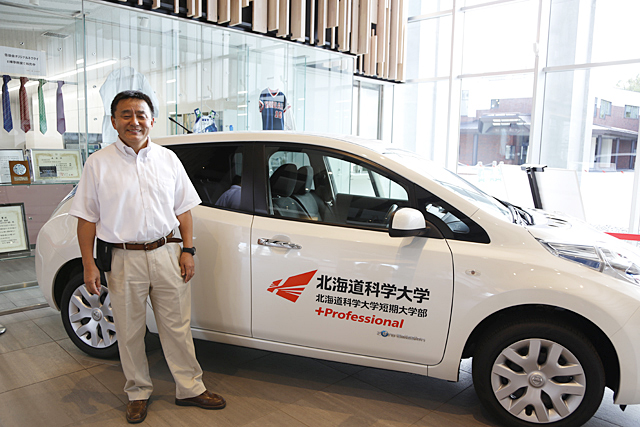
成型と廃棄が繊維強化プラスチックの課題
Q:繊維強化プラスチックの課題などはありますか。
太田:1つは作り方、成型の問題。もう1つは廃棄の問題ですね。 熱硬化性樹脂を成型するには、例えば加熱する前に余熱をかけたり、硬化温度で数時間加熱した後に24時間冷やすといった工程が必要で、1つの部品を作るのに1〜2日というサイクルでしか作れません。熱硬化性樹脂は金属の代替材料としては非常に性能が良いのですが、大量生産に踏み切れないため、現在は主に飛行機の胴体や翼などに使用されています。対して、熱可塑性樹脂は短時間で大量生産ができるので、現在自動車の部品などへの利用が進んでいるなど注目されています。
もう1つの課題が、廃棄の問題です。繊維強化プラスチックはその性質上硬くて耐熱性・耐久性に優れているため、処理をするのも非常に大変なのです。繊維強化プラスチックを切り刻んで道路のコンクリートの砂利替わりに使用する試みもあるようですが、繊維強化プラスチックが頑丈すぎて、リサイクルするにも非常にコストがかかってしまうのが難点です。
しかし今は廃棄の問題より先に、地球環境のためCO2を削減したい、車をなるべく軽くしたいという理由で繊維強化プラスチックを使おうという動きが活発化しています。繊維強化プラスチックの性能が良いことは分かっているので、今後はそれをどのように活かすのか、廃棄をどのようにしていくのかが課題となります。
Q:繊維強化プラスチックの最近のトレンドなどありましたらお聞かせください。
太田:繊維強化プラスチックは繊維方向への引っ張りには非常に強いのですが、繊維とは直角になる方向への引っ張りには弱いので、繊維の方向を色々な方向にすることで理想的な部品を作るような研究も進めています。
現在、3Dプリンターで繊維強化プラスチックを作るというのが世界的な1つのトレンドなのですが、これを使うことで、繊維の方向を複雑に変えた繊維強化プラスチックも簡単に作れるのです。これがどのような分野に活用できるかも含めて研究中ですが、とても楽しいですね。
日本は今まで大手企業でしか作れない高度な機械部品を製造していて、その技術を保有しているのが企業の利点でした。しかし、海外の企業には別の考えを持っていて、例えば3Dプリンターを購入すれば町の工場でも凄い部品が作れますよ、と生産システムも含めた展開を考えているようです。つまり、部品を3Dプリンターを用いて作りたくなったらCADで部品の図面を描き、自分の会社の近くにある町工場をネットで検索し、複数の工場で相見積もりを出した上で条件が良い所に部品を作ってもらう。そのような状況が近い将来訪れるかもしれません。
――後編では、引き続き北海道科学大学の太田教授に、研究を続ける醍醐味今後の展望に加え、学生へのユニークな指導方針、就職支援の方法についてお聞きします。
(プロフィール)
北海道科学大学
就職支援センター長・国際交流委員長
工学部 機械工学科 教授
文部科学省 科学技術・学術審議会 専門委員
工学博士
太田 佳樹
■北海道科学大学
https://www.hus.ac.jp/